生产物流配送最优批次模拟与诊断
生产物流配送最优批次模拟与诊断
文章作者:环球物流咨询首席咨询顾问——黄尧笛
在对于工厂生产物流体系进行系统性的模拟与诊断中,“最优”生产配送批次的模拟与诊断分析是必不可少的一部分。而“最优”生产配送批次的分析是一项具有挑战的工作,通常情况下规划人员会采用定性的方式进行规划设计。在本文中从实际案例出发,采用基于某工厂现实环境中的实体,在计算机中搭建其虚拟场景,再通过对真实作业活动的逻辑进行模拟,以输出不同配送批次下的作业效率和资源投入结果,供物流规划决策。此方法供参考
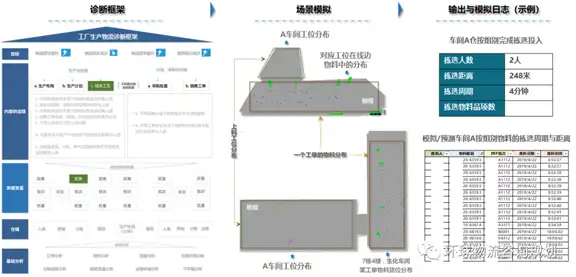
一、配送要素分析框架
工厂生产配送分析框架中,分别从流动性、配送网络、需求拉动、配送设计、管理与控制几个维度进行细节要素的分析。将分析的结果输入到场景中,进行系统性的仿真模拟。
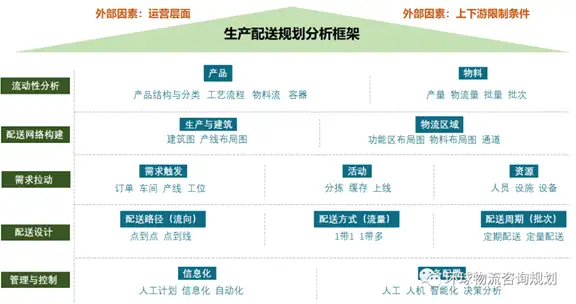
二、场景构建
将工厂生产物流体系构建在一个三维场景的坐标系中,在下图场景中,物料种类数3万种,每种物料按当前环境分配一个储位。车间工位按组别构成,一共1000个组别。根据当前的流程,由组别向原料仓储发起物料需求。

三、对场景模拟分析
对所有产线工位分批次叫料的情形下,触发工位与仓储物料分布位置以及资源使用数据的模拟(下图模拟批次为每天1-10个批次,可根据实际情况设置)。
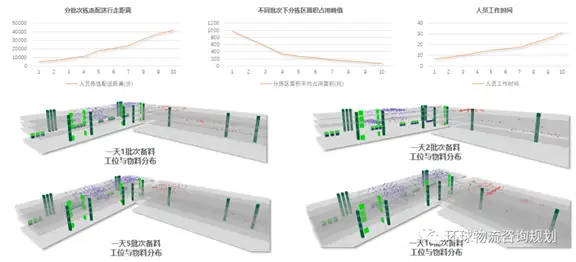
四、数据模拟结果输出示例
如下图,车间A当前按组别结构(线体工艺)下的拣选模式中,原料仓中完成一个组别拣选,平均2人,拣选总距离248米,拣选总周期4分钟。
如下图,车间A当前按组别结构(线体工艺)下的拣选模式中,原料仓中完成一个工单拣选,平均11人,拣选总距离4.17公里,拣选总周期1.9小时。
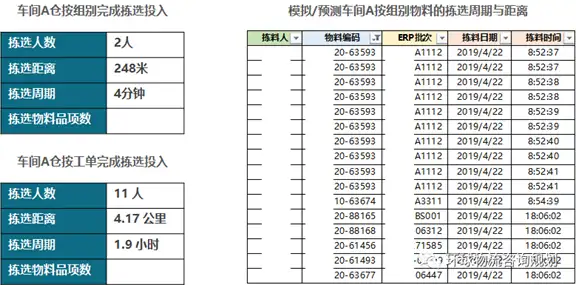
全部 0条评论