Modernization at Boscov’s
Boscov’s Department Stores DC makes gains from new sortation, controls and software plus racked order processing area.
Boscov’s Department Stores
- Location: Reading, Pa.
- Size: 395,000 square feet, plus attached 85,000 square feet building for stock replenishment.
- Products Handled: apparel, home goods, furniture, bedding, luggage, seasonal items.
- Throughput: 270,000 cases per week outbound, in peak seasons.
- Employees: 225, on average. Shifts: One 12-hour shift, five days a week.
Learn more about the Boscov distribution center.
Boscov’s DC in Reading, Pa., has long made heavy use of advance ship notices (ASNs) to support crossdocking of goods for specific stores, with 86% of cartons having an ASN. Between store-specific labeling and the ASNs, many cartons, especially during peak seasons, flow right through the facility. During non-peak times, there is relatively less flow-through and more order processing activity.
Inbound shipments arrive at one of 35 receiving doors (1), mainly as floor-loaded cartons, though a small percentage of cartons arrive in containers, and a small volume of palletized goods are also received. The operation uses extendable conveyors that reach into the floor-loaded trailers to make unloading easier. These extendable conveyors flow into multiple inbound conveyors that move cartons to a pre-sorter system (2) toward the center of the facility, or to sorter C. Each have a scan tunnel immediately upstream from it to read labels and route goods accordingly.

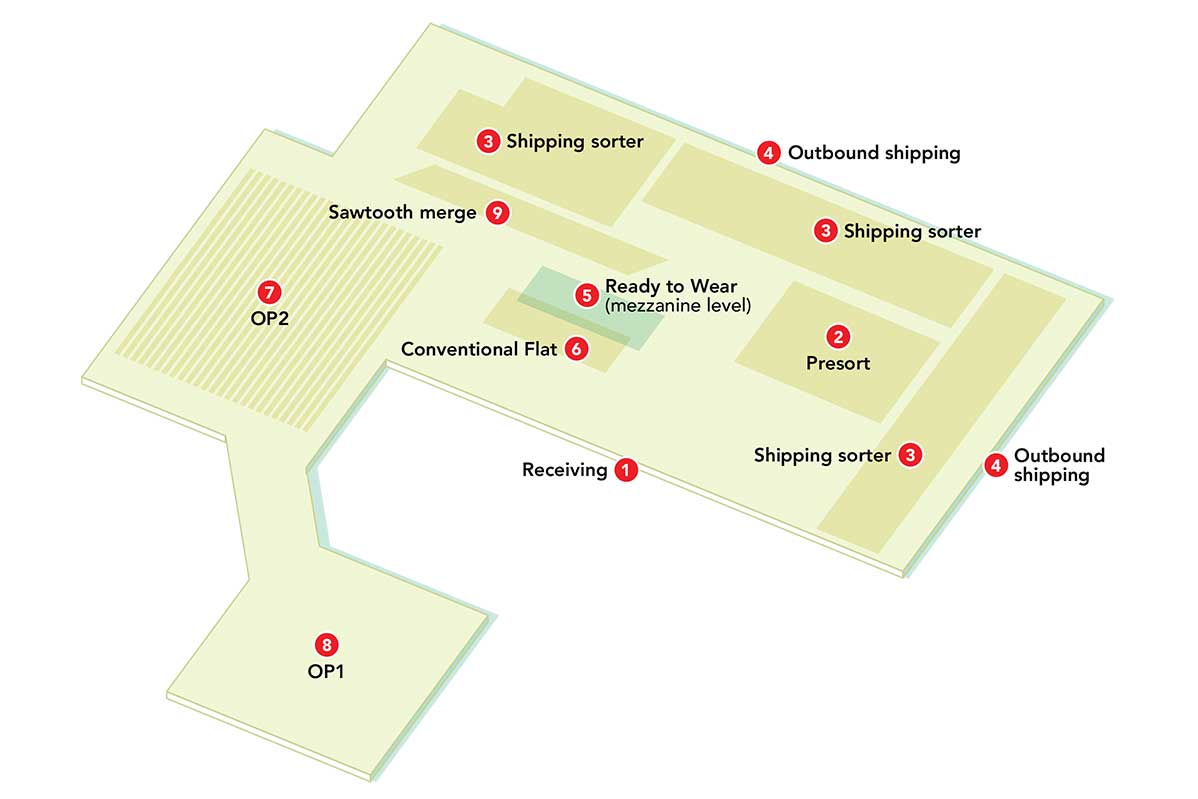
These two sorters will either route cartons to one of the outbound shipping sorters (3), or to one of the DC’s order processing areas it services, if order picking from stock, repacking or quality control steps are needed. The latest project upgraded one shoe sorter (sorter C) that can either route goods toward another shipping sorter route, or around to one of the value-added processing areas in the DC. This upgraded sorter, with additional diverts and conveyor path re-routing, added redundancy to outbound sortation, as well more flexibility for circulating cartons to order processing areas. The DC currently has 62 outbound shipping docks (4) along two sides of the main building.
The processing areas execute value-added services like taking goods out of cartons and repacking items as ready-to-wear products. They also handle quality control checks.
Two of these essential processing areas are located at the center of the main building, close to receiving, on two levels, one right over the other. On the ground level is Conventional Flat (6) where various services like repacking or labeling take place. A Ready-to-Wear processing area (5), located upstairs, provides item preparation, check-in, and processing onto the GOH system (garment on hanger).
The project added, using existing space, a new order processing area with racked storage, known as OP2 (7). This area provides easy access to goods that need to be held over the short to mid-term, using software to drive the order picking, as well as manually operated, narrow-aisle orderpickers for larger items or for pallet moves, and pick-to-cart for smaller items. Compared to dealing with goods stored in trailers, the reduced touches have significantly improved efficiencies in the DC. A pre-existing reserve storage area known as OP1 (8), remains in use and connected by conveyor to the other processes.
Nearly all the existing conveyor and sortation hardware, and all the five-sided scan tunnels, were replaced with new equipment, including programmable logic controllers (PLCs) and other key parts of the controls layer. A key addition was a new sawtooth merge (9) that brings together six lanes of goods coming from receiving and processing areas, to feed the new sorter C at a higher rate. The merge provides a pull system that allows upstream accumulation conveyor, feeding from the various areas, to operate without backing up the processing areas. The induct and sortation on sorter C operate with minimal gaps and are designed to handle a rate planned for several years in the future.
System suppliers
- Systems Integration: DLN Integrated Systems
- Sawtooth Sorter: Honeywell Intelligrated
- Controls/PLCs: Rockwell Automation
- WCS/WES: DLN Integrated Systems
- Scan Tunnel Technology: DataLogic
- Handheld Scanners: Zebra Technologies
- Rack Design and Install: Lift, Inc.
- Lift Trucks/Orderpickers: Crown
全部 0条评论