Efficiency across pallet and carton fulfillment workflows at Hamilton Beach
Hamilton Beach’s new distribution center in Byhalia, Mississippi, is a modern, omni-channel facility with 98 dock positions, utilizing advanced storage systems and processes to efficiently handle retail replenishment, e-commerce orders, and international distribution for its Mexico and Canada DCs.
Hamilton Beach
- Location: Byhalia, Miss.
- PRODUCTS HANDLED: Kitchen and home appliances SKUS: About 4,000, but varies with peak seasonality
- NUMBER OF EMPLOYEES: 275-325, depending on seasonality
- NUMBER OF SHIFTS: Two shifts per day Monday-Thursday; one shift per day, Friday-Sunday.
- SQUARE FOOTAGE: 1 million square feet
- THROUGHPUT: Non-peak, 5,000 to 7,500 pallets ship weekly, but as many as 12,000 pallets during peak times.
Hamilton Beach’s hub DC in Byhalia, Miss., near Memphis, is an omni-channel facility with international reach that fulfills orders for retail replenishment, e-commerce orders, and also distributes some palletized goods to Hamilton’s Beach DCs in Mexico and Canada. The site is a greenfield DC, opened in July 2021, replacing a slightly larger legacy site that stored palletized goods on floor locations.
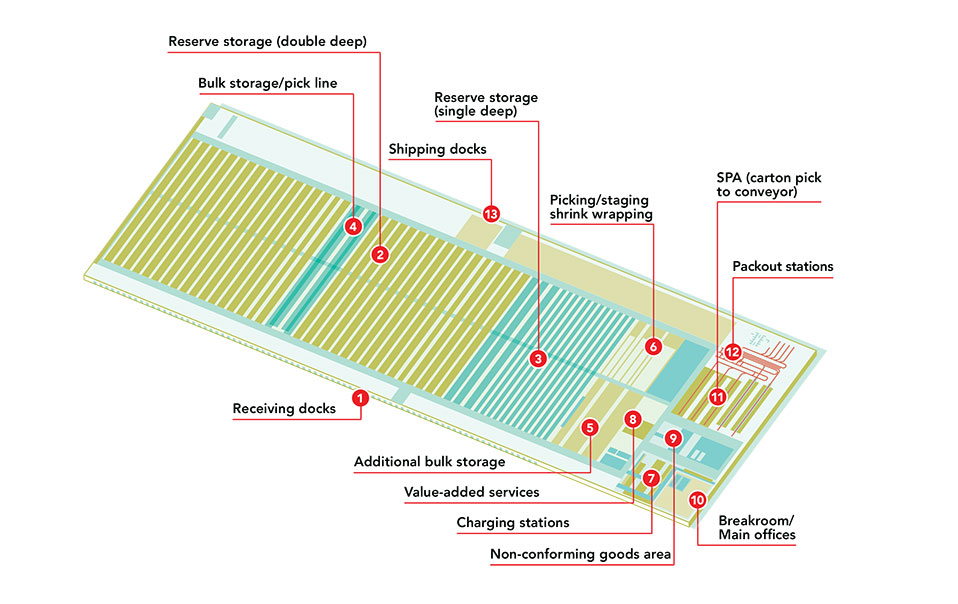
The new DC has 98 dock positions in its receiving area (1) along the south side of the DC. Most goods arrive floor loaded in containers and are manually palletized by lumpers prior to checking, count verification, receipt and staging for putaway using lift trucks.
Most goods are stored in double deep rack (20% of rack is single deep; 80% double deep) in the DC’s reserve storage area (2). This provides higher density for fast-moving SKUs often ordered in multiple pallets (the trucks use double deep forks, to permit handling of two pallets in one move), while the single deep rack (3) is positioned relatively closer to the carton picking area for ease of replenishment. A bulk storage area with a pick line through it (4) handles special pallet builds for some major retail customers.
The site has an additional bulk storage area (5) to the right on single-deep reserve storage staging and also, an open processing area for tasks including picking mixed SKU pallets and wrapping, prepping and staging orders for shipment (6). The opportunity charging stations (7) for site’s lift truck fleet is located near the break room and the site’s main office space (10). A value-added processing area (8) handles special orders, and there is also an area for handling non-conforming goods or loads (9).
The new site has a zoned, pick to conveyor system (11) in what the DC calls its small parcel area (SPA). This system uses zone picking logic to minimize associate travel, with rack to hold goods along the system. The conveyor automatically moves picked parcels to packout stations (12) downstream. The parcel carrier dock doors are located in the upper right corner of the DC, near SPA.
The north side of the facility is shipping (13), with 100 dock positions to handle full truckload, less than truckload, and parcel shipping needs. The north side of the DC also has a wide lane for staging and loading activity, adjacent to the dock positions.
System suppliers
- Yale Lift Truck Technologies - Lift trucks
- Elite Storage Solutions/Nucor - Rack
- Körber Supply Chain - Warehouse management system
- Adaptec Solutions - Conveyor
全部 0条评论