自动化物流系统在铸造企业中的应用与实践
铸造行业多属于离散型生产模式,要实现智能工厂基本是难上加难。延伸到物流系统,由于工序多样化和稳定性的影响,就使实现全自动的目标相比较其他产业需求更加复杂,不论是对硬件的基本配置要求还是软件的逻辑算法,都提出了新的要求。本文通过总结智能工厂自动物流系统建设过程,提炼了建设过程中的要点和经验。
在铸造行业,由于离散型生产、工序标准化差等因素影响,在智能制造方面始终无大的突破。共享智能铸造产业创新中心有限公司结合多年铸造行业生产经验,积极投入大量人力物力在铸造生产自动化方面进行实践研发,实现了自动化工厂的建设投产,在铸造行业产业升级的道路上踏出了坚实的一步。
一、自动物流系统简介
物流自动化是充分利用各种机械和运输设备、计算机系统和综合作业协调等技术手段,通过对物流系统的整体规划及技术应用,使物流的相关作业和内容省力化、效率化、合理化,快速、精准、可靠地完成物流的过程。
物流自动化在物流管理各个层次中发挥重要的作用。它包括物流规划、物流信息技术及自动物流系统等各种软技术和硬技术,其主要硬件内容包括RGV、AGV、辊道线、堆垛机、立体库等。
二、全自动物流系统在共享集团智能工厂项目中的实际应用
在自动化工厂现场,采用RGV+辊道线+立体库+工作缓存工位+智能单元控制系统组成全自动物流系统。为减轻工人的劳动强度、降低在转运时受伤的风险、提升工作效率、完成自动化工厂建设运行的目标,全自动RGV设备以及与其搭载的相关智能化系统与平台被应用到工厂中,代替之前的叉车、天车等需要人工操作的转运工具进行工作物流工作,实现自动化智能化目标。
1.大件造型:100t重载RGV车从搭建组芯处承载托盘,经过铺底砂、下芯、合箱、加围砂等工序,运送至等待浇铸工位,浇铸后运输至缓存工位等待冷箱,可开箱砂箱运输至开箱工位进行开箱,空箱运输至缓存工位,等待下一次流程。
2.砂箱运输:RGV穿梭车将满箱砂箱从3D打印机运输至满箱缓存线,清砂站满箱呼叫后,RGV穿梭车将满箱砂箱运输至清砂站,空箱由RGV穿梭车运输至缓存线或3D打印机。
3.小件砂型运输:立体库将小件砂芯运输至转运RGV上,由转运RGV车转运至人工组芯台,人工组芯完成后,由转运RGV运输至缓存线,再由运输砂型的RGV运输至小件合箱处合箱。
4.立体库:堆垛机将托盘从入库位置运输至立体库内指定位置,再将空托盘转运至出库位置。
5.工作缓存工位:在标准工序之间或标准工序位置上,通过标准砂箱或标准托盘为载体,通过RGV运输,送达指定坐标点位。
共享智能铸造产业创新中心有限公司优化采用AGV+RGV+辊道线+立体库+智能单元控制的方案,实现从3D打印设备到缓存工位,缓存工位到清砂工位,以及最终入立体库储存的全自动控制应用,物流效率质量均得到大幅的提升。
三、全自动物流系统及RGV/AGV在现场应用的关键点
一个好的系统,具有稳定、高效的特点,而要保证这些目标的实现,在建设和使用过程中,要抓住其中的一些关键点,重点关注。
1.可靠的网络及检测反馈系统
有别于传统的物流系统采用固定限位或人的跟踪控制,自动物流系统通过实时位置的检测反馈,来控制动作的运行和到位与否。检测信号不稳定,就会导致系统判断不能运行,或者更严重的物流不受系统控制的运行,以致严重的设备安全事故发生。以下两方面的工作要求必须要做好:
一方面,工厂现场及整个检测反馈系统,尤其是安装在现场的系统,必须得到很好的现场检查维护清洁工作。也就是现场的6S工作标准,智能工厂比普通工厂应该执行更严格的要求。尤其是在物流系统,其大部分是运动部件,异常往往会导致很大的损失。
另一方面,以物流线的运行要求,反推上线设计产品的标准化,对非标、超标的情况,一定要在设计阶段解决问题,保证系统安全稳定地运行。
2.合理优化的系统自运算逻辑设计
有别于传统刚性生产线或成熟汽车行业生产线的要求,铸造行业运行的要求是柔性化的,在工艺流程、合格标准、处理的方法等要求上,都有更多的选择和工况,这就决定了柔性自动生产线面对更多的选择和更多的工况,就要设计更多、更合理的系统自运算逻辑,当逻辑覆盖不全或判断不合适,都会造成系统计算错误或进入死循环,导致整个自动运行系统的停止。
3.持续稳定的应用更考验综合保障能力
有别于传统的现场生产组织方式,各个工序职责明确,包括生产准备、检验、报工等辅助配合工作。而自动生产系统,则需要以自动线为核心,拉动相关工作按时完成,甚至超前完成。
从质量方面,硬件的固化,更增大了质量标准和过程标准的提高,这就是对我们过程工作质量有了更高的要求,把最终的质量目标,分解到各个环节,标准化生产,整体能力提高来保证最终的质量水平。
4.缓存工位设置的必要性
柔性生产线,区别于刚性生产线的地方就在于其节拍的不平衡性,比如说制芯序,是一个个砂芯进行生产组织,但到了组芯序,就需要一组砂芯同时进入工作位进行操作处理,再有就是不同的产品节拍时间也不一样,对于离散型生产方式,需要较高频率的换产品,组织生产。这些都给实现连续自动运行造成了很大的影响。
因此在关键工序间设置缓存工位,就可以在一定程度上缓解处理由以上因素造成的影响。
四、自动物流系统对现场效率的影响
1.未使用全自动的现场物流效率
现场物流效率由工人操作熟练度决定,平均每个流程时间在15分钟以上,并且易出现操作失误以及位置冲突等问题,造成时间浪费现象。
2.使用全自动RGV/AGV的现场物流效率
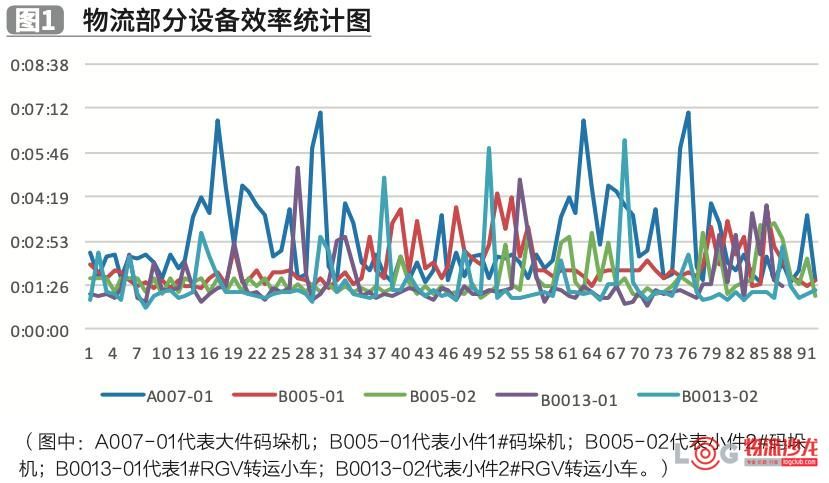
如图1可以看出:
(1)除现场多任务重叠时造成部分转运时间较长(4分钟以上)外,其他时间段内转运时间均在2分钟左右;
(2)现场实测,非自动化码垛机入库托盘时间较长,一个流程平均时间20分钟;
(3)两辆转运小车时间过长时,相应码垛机运行时间短,这由于现场存在小车等待码垛机流程现象,反之也是;
(4)物流设备无停机时间,24小时运行。
综合以上数据,可以得出以下结论:
(1)全自动物流系统大大缩短了每个流程所需要的时间;
(2)全自动物流系统在使用时,不会出现流程冲突现象(等待流程属于正常现象,不属于流程冲突;流程冲突是指两流程运行时严重干涉,导致所有流程无法进行的现象);
(3)全自动物流系统无停机时刻,全天候工作。
五、结论
全自动物流系统的使用,很好地提高了现场的物流系统效率,对铸造车间提质增效的目标起了极大的促进作用。
以物流系统为桥梁,一方面连接起了各个工序,使过去传统的单工序离散管理改变为工作流全面管理。另一方面以自动运行流程为抓手,反向拉动工序标准化、质量标准化,对企业的整体实力影响深远。
文|共享智能铸造产业创新中心有限公司
全部 0条评论